Revolutionizing the Assembly Line: Honda’s Breakthrough Welding Method Redefines Car Manufacturing
Imagine a world where cars are not only faster, safer, and more efficient, but also more resilient and durable. Welcome to the future of automotive manufacturing, where Honda is pioneering a game-changing technology that’s transforming the way cars are built from the ground up. In a groundbreaking move, the Japanese auto giant has introduced a cutting-edge welding method that’s redefining the industry’s standards for quality, precision, and sustainability.
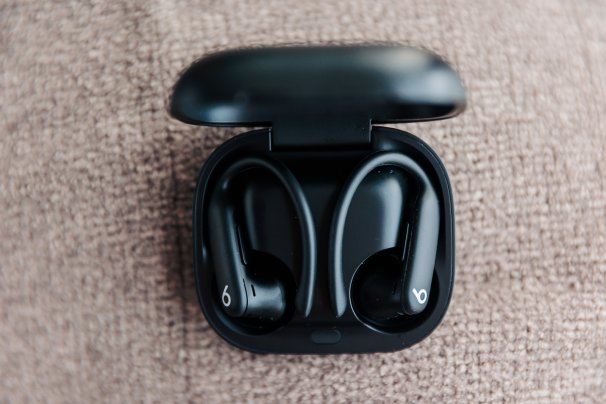
The Transformation of the Marysville Plant
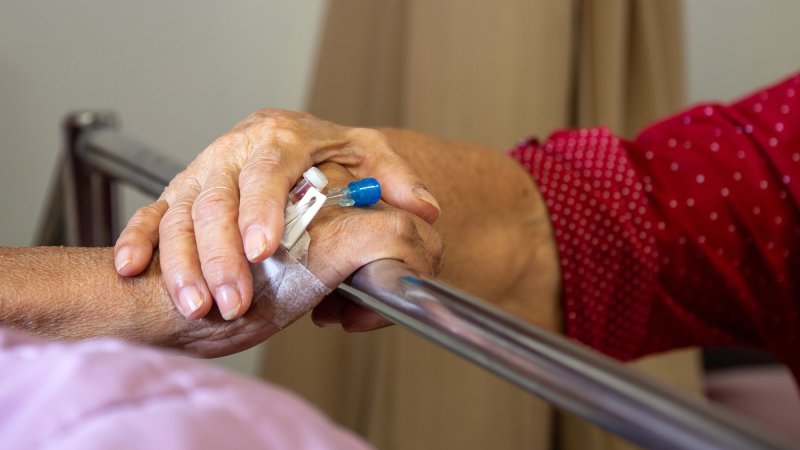
Honda’s ambitious $1 billion investment to retool its Ohio facilities signals a commitment to a flexible future in automotive manufacturing. The Marysville plant, along with its nearby counterparts in Anna and East Liberty, is undergoing a transformation to accommodate a diverse range of vehicles, including the upcoming Acura RSX SUV, Honda 0 Saloon, and Honda 0 SUV prototypes.
This strategic shift reflects Honda’s “thin, light, and wise” strategy, aiming to produce internal combustion, hybrid-electric, and battery-electric vehicles on the same production lines. This flexibility allows Honda to adapt to changing market demands and consumer preferences.
From ICE to EV
The Marysville plant has a rich history, beginning with the iconic Gold Wing motorcycle production in the 1970s and transitioning to Accord sedans in 1982. Today, as Honda strives for 100% zero-emissions vehicle sales by 2040, the plant is at the forefront of this transition.
The new line at Marysville will debut with the battery-electric Acura RSX SUV later this year, followed by production models of the Honda 0 Saloon and Honda 0 SUV. This marks a significant step towards electrifying Honda’s lineup and establishing a hub for EV manufacturing in Ohio.
A Hub for Innovation
Central to this transformation is the integration of a novel welding process called CDC (constant DC chopping) welding. This innovative technique represents a significant advancement in automotive manufacturing, offering several benefits over traditional methods.
CDC Welding: The Science Behind the Strength
Honda’s CDC welding process combines the strengths of both DC and AC welding techniques to achieve superior weld quality and efficiency.
Understanding the Technology
Traditionally, spot welding utilizes a constant current to generate heat and fuse metal together. However, Honda’s CDC method introduces a “chopping” action to the current flow, precisely controlling the nugget temperature and penetration.
This constant DC chopping, alongside a high peak current and automatic pause time control, ensures consistent heat distribution and optimal weld strength. By manipulating the current waveform, technicians can achieve precise control over the welding process.
Benefits of CDC
The CDC welding process offers several advantages over conventional methods, particularly when joining metals of varying thicknesses:
- Improved Weld Quality: CDC welding ensures full penetration and superior strength, even when welding dissimilar metals.
- Reduced Distortion: The precise control over heat distribution minimizes metal warping and distortion during the welding process.
- Enhanced Efficiency: The optimized welding parameters reduce cycle times and increase overall production efficiency.
Global Impact
The implementation of CDC welding in Honda’s high-volume manufacturing represents a significant milestone. It signifies Honda’s commitment to innovation and its willingness to adopt cutting-edge technologies to enhance its manufacturing processes.
This approach has the potential to revolutionize automotive welding practices, setting a new standard for quality and efficiency across the industry.
Conclusion
In conclusion, Honda’s innovative welding method is revolutionizing its car manufacturing process, redefining the industry’s standards for quality, efficiency, and precision. As discussed in the article, this cutting-edge technology has enabled Honda to significantly reduce production time, minimize labor costs, and produce vehicles with unparalleled strength and durability. The key takeaway is that this method’s impact extends far beyond the factory floor, as it has the potential to transform the entire automotive industry.
The significance of Honda’s welding method lies in its ability to set a new benchmark for manufacturing excellence. As the demand for sustainable, high-quality vehicles continues to grow, this technology offers a promising solution for manufacturers seeking to optimize their production processes. Moreover, this innovation has far-reaching implications for the environment, as it enables the production of lighter, more fuel-efficient vehicles that reduce carbon emissions. With its potential to transform the industry, Honda’s welding method is poised to shape the future of the automotive sector.
As we look to the future, it’s clear that Honda’s pioneering spirit will continue to drive innovation and progress. As the industry continues to evolve, it will be exciting to see how this technology is adapted and improved upon. One thing is certain, however – the future of car manufacturing has never looked brighter, and Honda’s special welding method is leading the charge. As we gaze into the horizon, it’s clear that the future of mobility is not just about the vehicles we drive, but about the innovative spirit that powers them.
Add Comment